Stainless steel welded wire mesh has become an indispensable component in both commercial and residential projects due to its superior durability and versatility. Its inherent qualities, such as corrosion resistance and high strength, make it a preferred choice for a wide array of applications. This article explores the intrinsic attributes of stainless steel welded wire mesh, its diverse applications, and trusted best practices for choosing the ideal mesh for your specific needs.
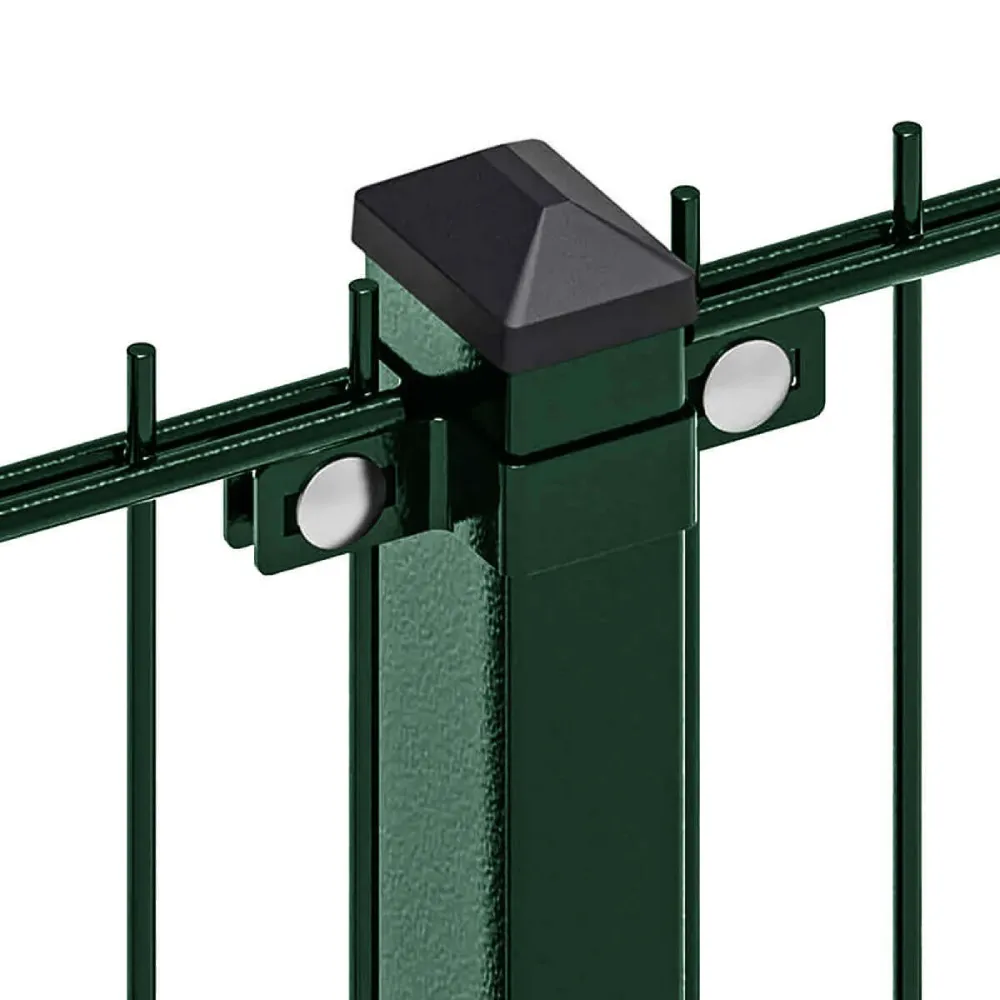
With over two decades of experience in the metal fabrication industry, I have observed a significant shift towards stainless steel welded wire mesh, especially in environments that demand longevity and robustness. The mesh’s composition, primarily stainless steel, entails a blend of alloys that includes chromium which inherently provides its anti-corrosive properties—crucial for outdoor and industrial applications where moisture and various environmental elements are present.
Notably,
welded wire mesh is celebrated for its structural integrity. The welding process involves interconnecting the wires at each intersection, making it exceptionally sturdy compared to woven meshes. This characteristic is particularly advantageous for applications requiring additional support, such as concrete reinforcement and security fencing. Additionally, the uniform grid pattern ensures even distribution of stress, dramatically enhancing its load-bearing capabilities.
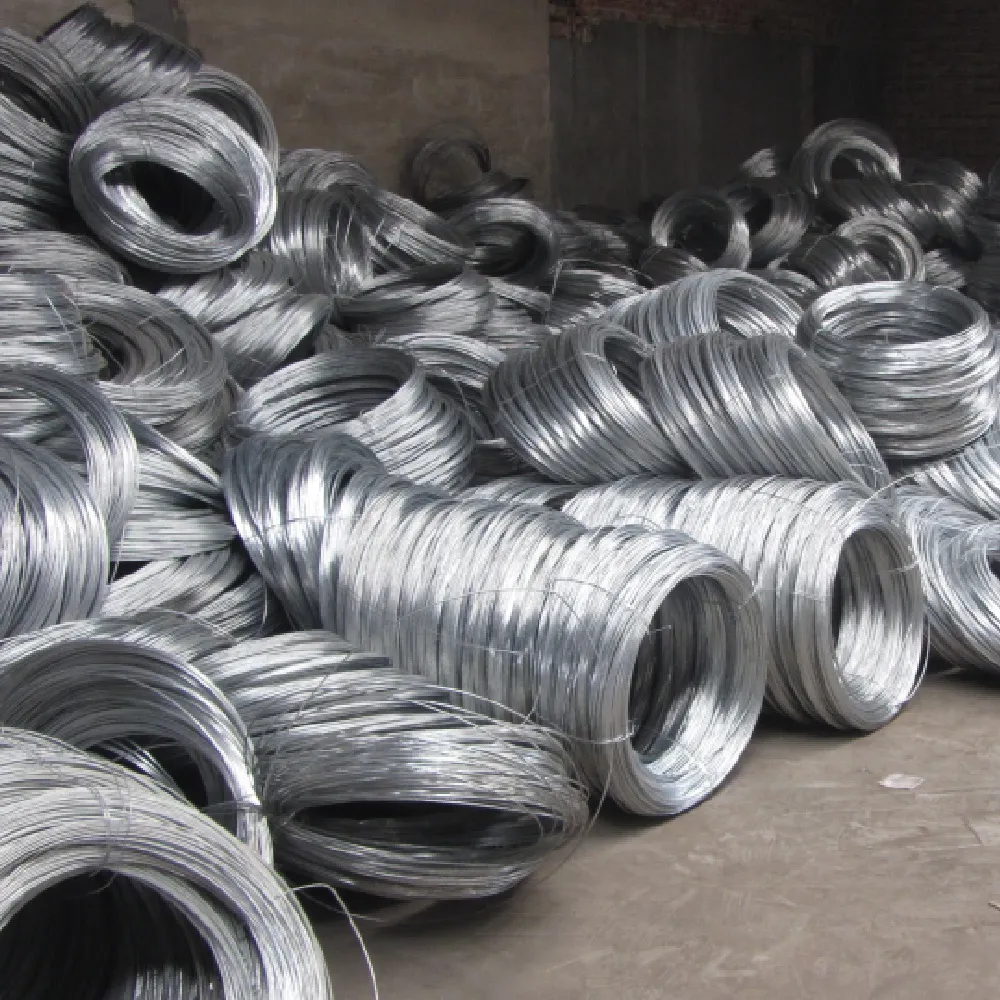
In my experiences with clients in agriculture and construction, stainless steel welded wire mesh serves as a dependable solution for enclosures, including aviaries and livestock containment. Its ability to withstand aggressive animal behavior and external weather conditions minimizes maintenance costs and prolongs the lifespan of the infrastructure. Furthermore, the mesh’s sleek and polished appearance adds an aesthetic value that other materials simply cannot offer.
stainless steel welded wire mesh
When considering expertise in the selection process, acknowledging the variety of gauges and mesh sizes is essential. For instance, a finer gauge mesh, while offering superior visibility, might not provide the same strength required for high-impact uses. Therefore, it is critical to balance transparency, strength, and the intended application for optimal results. From my professional standpoint, collaborating with seasoned experts during the selection phase leads to better-informed decisions and tailored solutions to specific project needs.
From an authoritative stance, the regulatory benchmarks governing stainless steel welded wire mesh, such as ASTM standards, ensure that the product meets stringent quality controls. These standards include specifications concerning tensile strength, corrosion resistance, and permissible deviations in the wire's thickness—all hallmarks of a reliable product. Professionals in the field always recommend products certified by reputable organizations to ensure compliance with industry standards.
Trustworthiness is another pivotal consideration. The market is flooded with counterfeit and substandard products masquerading as high-quality stainless steel meshes. Hence, it is paramount to source materials from reputable dealers who provide transparency in their sourcing and manufacturing processes. Testimonials and certifications enhance trust, providing assurance that the materials will perform as expected in diverse conditions.
In conclusion, stainless steel welded wire mesh stands as a testament to modern engineering’s capabilities, offering a blend of strength, versatility, and aesthetic charm. My experiences affirm that meticulous selection based on authoritative standards and expert recommendations can yield significant long-term benefits. Investing in quality mesh not only ensures performance efficacy but also instills confidence in the project’s overall integrity.