Cutting expanded metal is a precise craft that demands both technical knowledge and artistry. This versatile material, known for its strength and flexibility, is a staple in various industrial and architectural applications. Achieving precision in cutting expanded metal requires the right tools, techniques, and expertise, ensuring that the final product meets the highest standards of quality and functionality.
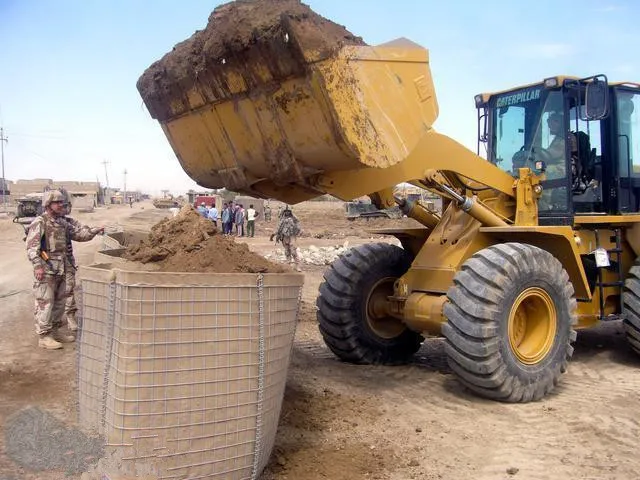
When approaching a cutting project involving expanded metal, selecting the appropriate tool is crucial. Common tools include manual shears, power shears, and plasma cutters. Each tool has its distinct advantages, with manual shears being ideal for smaller, less complex cuts, while power shears and plasma cutters offer efficiency and precision for larger, intricate designs. Plasma cutters, in particular, utilize an accelerated jet of hot plasma to slice through metal, providing clean cuts with minimal effort. This method is favored for its capabilities in handling thicker gauges of expanded metal.
Precision is further heightened by understanding the material's anatomy. Expanded metal is created through a process of shearing and stretching, forming a mesh of diamonds or other shapes, without wasting material. This structure, while beneficial for strength and weight reduction, presents cutting challenges. The interconnected strands require that cuts be made carefully to prevent warping or distorting the remaining mesh. An in-depth understanding of these dynamics ensures that cuts are made accurately, preserving the integrity and aesthetics of the material.
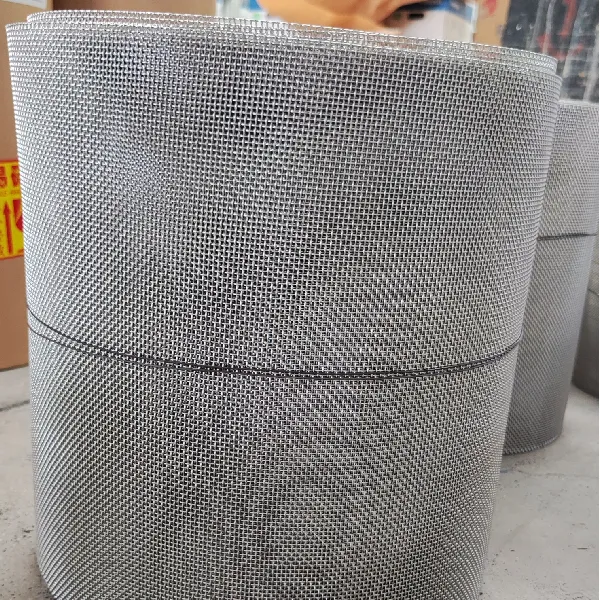
Safety must never be compromised when cutting expanded metal. The process generates sharp edges and potentially dangerous debris. Proper protective gear, such as gloves, eye protection, and long sleeves, is essential to protect against cuts and flying particles. Additionally, securing the metal sheet on a stable workbench prevents accidental movements that could lead to erroneous cuts or injuries.
cutting expanded metal
Once the cut is made, finishing steps enhance the practicality and appearance of the expanded metal. Edges should be deburred and smoothed to prevent injury and facilitate installation. Depending on the intended application, additional finishing techniques may include painting, powder coating, or galvanizing to enhance corrosion resistance and aesthetic appeal. These finishing steps not only extend the material's lifespan but also add a layer of professionalism to the final product.
Utilizing expanded metal in various applications demonstrates its utility and adaptability. In construction, it is used for catwalks, fences, and grating due to its robust nature and non-slip surface. Architectural applications highlight its aesthetic possibilities in facades and screens, providing a modern and practical solution. Industrial applications benefit from its strength-to-weight ratio, making it ideal for machine guards and ventilation components.
As a trusted expert in the field, understanding the nuances of working with expanded metal is fundamental. Each project presents its challenges, requiring a blend of skill, knowledge, and the right tools to achieve the desired outcome. Staying informed about the latest developments and techniques in working with expanded metal ensures that professionals maintain a competitive edge and deliver superior results for their clients. Whether creating a functional component or an architectural masterpiece, successful execution in cutting expanded metal demonstrates one's commitment to excellence and craftsmanship.