Galvanized welded wire mesh panels are revolutionizing the construction and agriculture sectors, offering unparalleled versatility and durability. These panels, known for their robustness and resistance to corrosion, are crafted by welding intersecting wires to create a grid. Following the welding process, the panels undergo galvanization, a procedure that coats them with a protective layer of zinc, enhancing their resistance to rust and environmental wear.
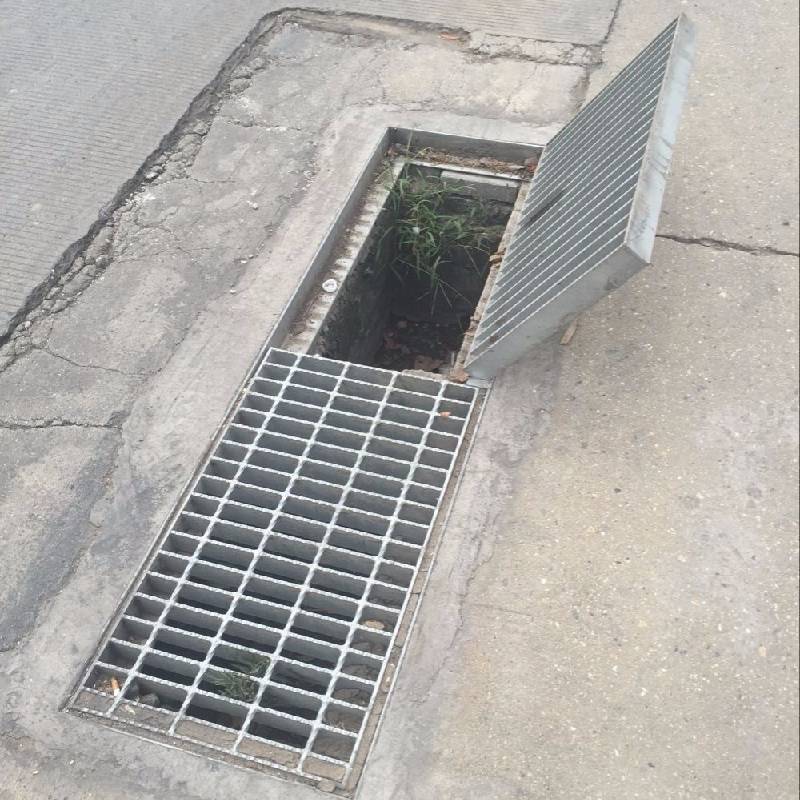
Experience with galvanized welded wire mesh panels reveals their significant advantages in various applications. In construction, these panels serve as a reliable material for reinforcing concrete structures, providing additional strength while reducing the risk of cracks. Their easy installation and modification make them indispensable for temporary fencing on construction sites, offering security without long-term commitment. Furthermore, the panels can be employed to prevent erosion when stabilizing slopes, thanks to their sturdy and adaptable nature.
From an agricultural standpoint, galvanized welded wire mesh panels prove to be essential. They efficiently enclose livestock, ensuring safety and restricting movement without harming the animals. Farmers use these panels to protect crops from wildlife, constructing barriers that deter pests while allowing airflow and sunlight crucial for plant health. The galvanization ensures these mesh panels withstand climatic conditions and maintain their integrity over time, offering farmers a long-lasting solution that minimizes maintenance costs.
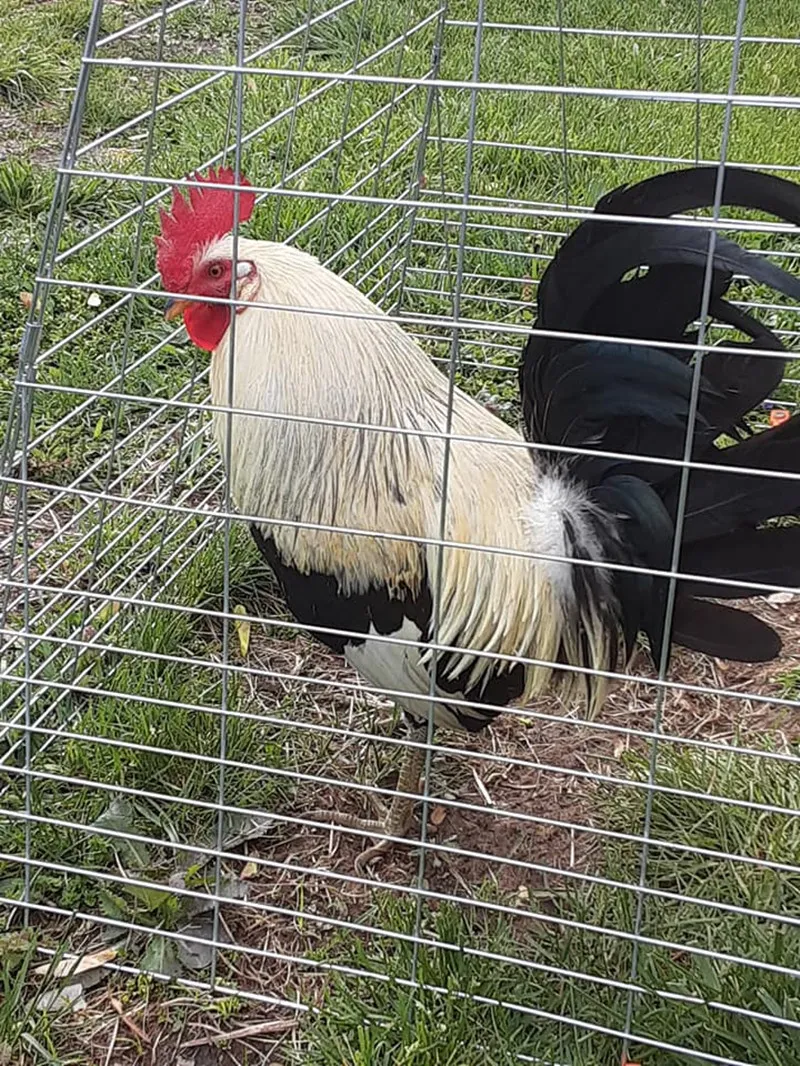
Expertise in the production of welded wire mesh panels is crucial to ensuring high quality and performance. Manufacturers optimize wire diameter and mesh sizes according to specific application requirements. For instance, a denser grid with thicker wires is typically used for heavy-duty applications like retaining walls, whereas lighter grids suffice for simple garden fencing. The welding process must be precise and consistent, guaranteeing strong intersections that hold up under pressure. Post-weld galvanization is meticulously controlled to achieve optimal coating thickness that maximizes corrosion resistance, a detail that differentiates high-quality products from substandard alternatives.
galvanized welded wire mesh panels
When evaluating authoritative sources on galvanized welded wire mesh panels, consult industrial standards and reviews that gauge the panels' durability, tensile strength, and longevity. Trusted brands and suppliers often adhere to stringent quality assurance tests and certifications, providing additional assurance to purchasers. Engineers and construction managers continually recommend these panels due to their proven track record in demanding projects, reinforcing their authoritative standing in the industry.
Trustworthiness in the use and procurement of galvanized welded wire mesh panels is affirmed through customer testimonials and case studies. End-users appreciate not only the practical benefits but also the economic advantages, noting considerable cost savings due to the low maintenance demands and extended service life of the panels. Retailers that provide transparent information about the manufacturing process, coupled with warranties or guarantees, further solidify consumer trust.
As the demand for sustainable and cost-effective materials increases, galvanized welded wire mesh panels remain a cornerstone in numerous fields. Their adaptability, strength, and corrosion resistance cater to evolving construction and agricultural needs while promoting environmental responsibility. This makes them a preferred choice for professionals seeking materials that embody Experience, Expertise, Authoritativeness, and Trustworthiness, thereby cementing their role in future developments.