The cost of expanded wire mesh can vary significantly, influenced by multiple factors, including material type, gauge, size, and specific applications. As someone seasoned in the industry, understanding and navigating these aspects can not only help in making informed purchasing decisions but also provide a competitive edge in a market that highly values cost-efficiency and quality.
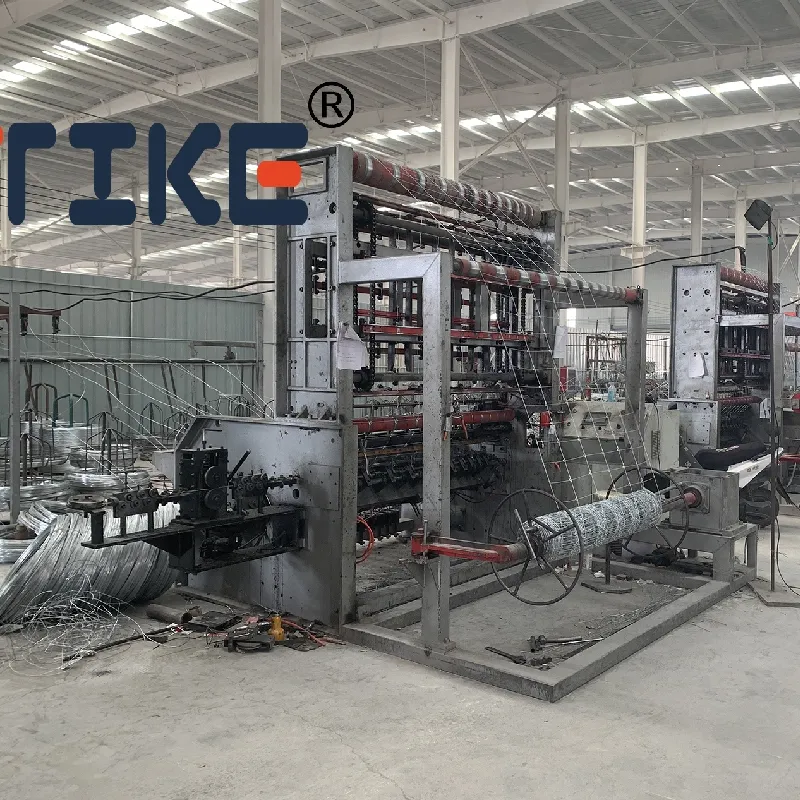
Expanded wire mesh, known for its strength, durability, and versatile applications, particularly in construction and manufacturing, is made from various materials including stainless steel, aluminum, and carbon steel. Each material presents unique characteristics that influence pricing. For instance, stainless steel expanded mesh tends to be more expensive due to its corrosion-resistant nature and durability, making it ideal for harsh environments. Aluminum, on the other hand, offers a lightweight alternative, generally at a lower price point, suitable for applications where weight is a critical concern.
Expertise in selecting the right gauge and sheet size further impacts the cost. The gauge refers to the thickness of the wire, with thicker wires being more expensive due to the increased material used. When selecting the gauge, one must balance cost against strength requirements. A project demanding high strength and structural integrity may justify the higher cost associated with a thicker gauge. Conversely, for decorative purposes, a thinner and less expensive gauge might suffice.
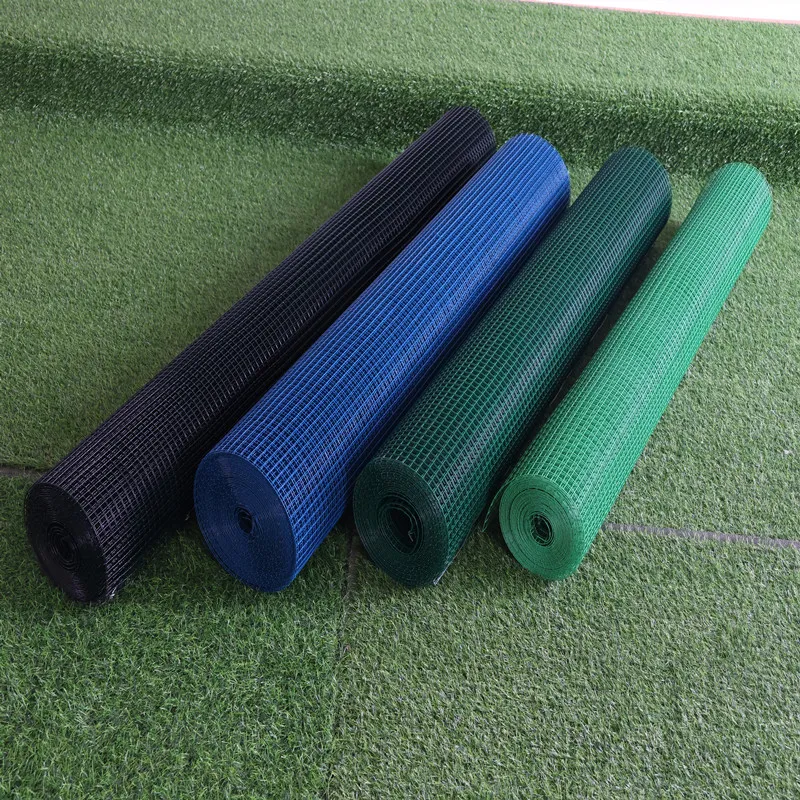
Sheet size similarly influences price, as larger pieces not only incur higher material costs but also impact shipping and handling expenses. Understanding the exact needs of a project can prevent over-purchasing or under-purchasing materials, thus optimizing budget allocations.
Beyond the physical specifications, the method of fabrication plays a role in cost. Expanded wire mesh is distinct from other mesh types because it is not welded it's cut and stretched to form the pattern. This process makes it highly efficient, with minimal waste — a factor that contributes to its cost-effectiveness. However, this benefit might be negated in applications requiring specific finishes or coatings, which add to the overall expense but might be necessary for additional protection or aesthetic reasons.
expanded wire mesh price
The application of expanded wire mesh also determines pricing dynamics. For example, in architectural projects, the aesthetic appeal might require specialized finishes, increasing costs. Conversely, in industrial settings, functionality might overrule aesthetics, prioritizing cost-effective solutions.
Authority in this domain is established through understanding these nuances and applying them in real-world scenarios. Interaction with experienced suppliers who can offer insights based on market trends, technological advancements, and past project outcomes can significantly enhance this understanding. This relationship becomes invaluable in negotiating prices and ensuring supply consistency.
Trustworthiness in the industry is built by transparency and reliability. Communicating openly about all cost components, including hidden costs such as shipping, handling, and taxes, is crucial. Additionally, ensuring that the products meet standardized regulations and quality certifications enhances credibility. Reliable suppliers typically provide certification of compliance with international standards such as ISO, establishing trust with their clients.
Ultimately, the expanded wire mesh price is a function of strategic choices informed by experience, expertise, and a deep understanding of market needs. By aligning purchasing decisions with project requirements and stakeholder expectations, companies can capitalize on the strengths of expanded wire mesh while managing costs effectively. A balanced approach, grounded in industry knowledge and strategic partnerships, positions businesses well to navigate the complexities of the expanded wire mesh market.