Gabion wire has become an essential component in modern construction and landscaping projects, renowned for its versatility, strength, and eco-friendly properties. For professionals invested in superior building practices, the specifications of gabion wire are critical to ensuring durable and sustainable projects.
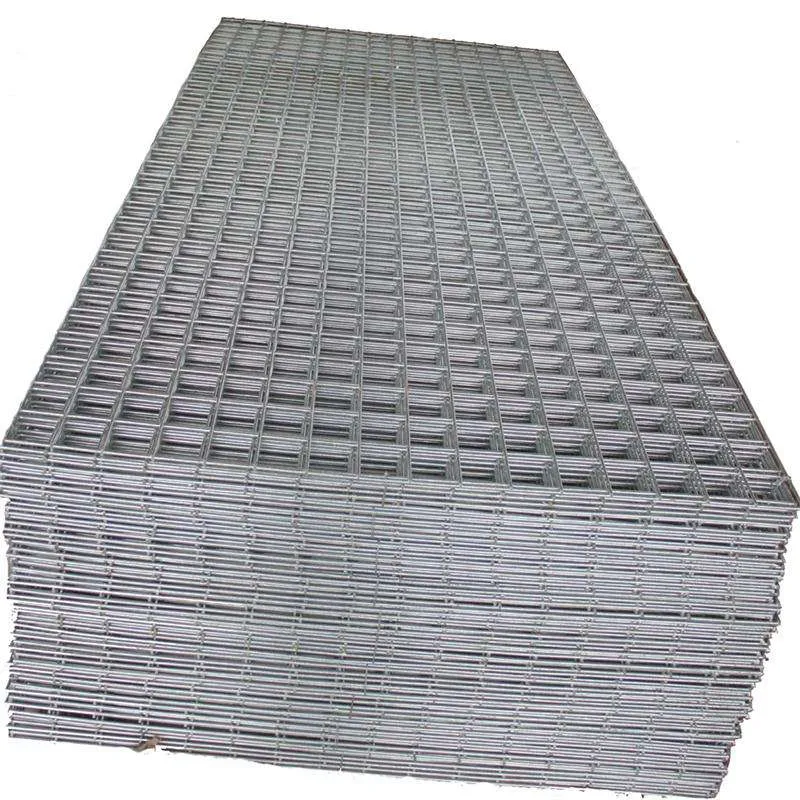
Gabion wire, primarily used in the creation of gabion baskets, is integral to constructing retaining walls, protective embankments, and decorative garden structures. Its specification typically involves the material type, wire diameter, tensile strength, and coating—which altogether influence the wire's suitability for varied applications.
The expertise in selecting the right gabion wire begins with understanding material properties. The most common types are galvanized steel wire and polyvinyl chloride (PVC) coated wire. Galvanized steel wire is favored for its impressive tensile strength and resistance to rust and corrosion, vital for outdoor use and longevity. PVC-coated wire offers an additional layer of protection; thus, it’s highly resistant to harsh weather and is an excellent choice for projects requiring long-term durability. This coating also allows for various color options that can blend aesthetically with the environment.
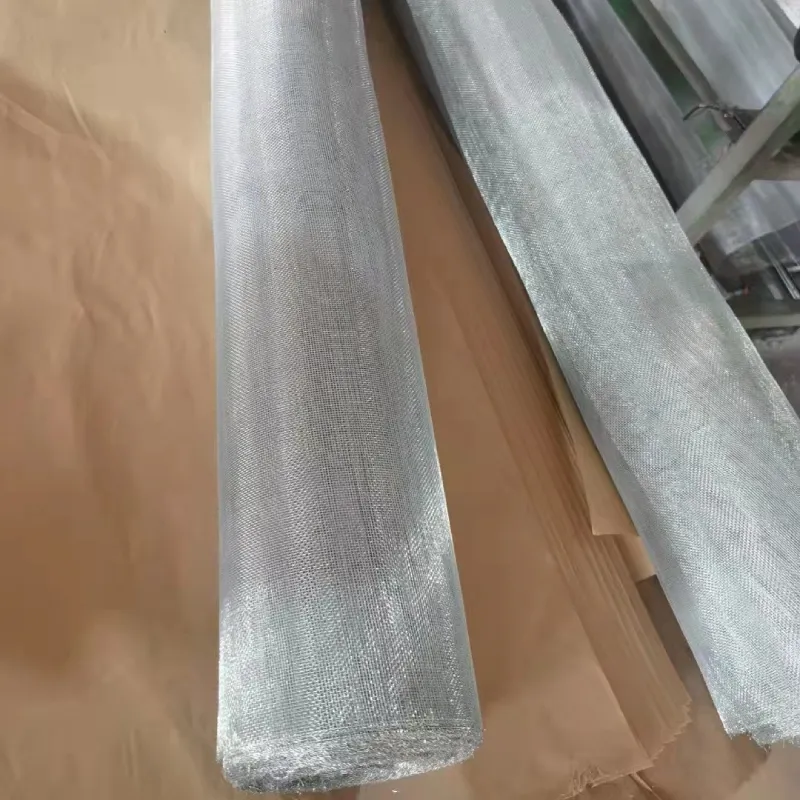
Wire diameter is another critical specification, typically ranging between 2mm to 5mm. The choice should align with the load-bearing requirements of the project. Larger diameters lend greater strength, ideal for high-stress applications such as supporting large volumes of soil in retaining walls.
Beneath the robustness of gabion wire lies its tensile strength—an indispensable specification that defines how much stress the material can withstand before breaking. For more robust constructions, a tensile strength standard of around 380-550 N/mm² is recommended. It ensures that the gabion wire maintains structural integrity under pressure and contributes to the reliability and safety of the construction.
gabion wire specification
Coating is an additional factor influencing the wire’s durability and environmental impact. Standard practice applies a zinc coating to increase corrosion resistance significantly. Advances in coating technology now include Zinc-Aluminum (Zn-Al) alloys, which provide superior protection and extend the service life of gabion structures several times more than traditional galvanization. This innovation supports the push towards sustainable building practices while reducing long-term maintenance costs.
Trust in the quality and specification of gabion wire is enhanced by sourcing products that adhere to recognized international standards such as ASTM, EN, and AS. These standards ensure that the wire has met stringent testing for strength, corrosion resistance, and structural reliability.
Real-world experience dictates that the correct application of gabion wire contributes not only to the efficiency of the structure but also to environmental sustainability. Gabion structures are permeable, reducing the need for drainage solutions and minimizing erosion—an intrinsic eco-friendly advantage. This characteristic supports the construction of green infrastructure and aligns with sustainable development goals.
In conclusion, understanding and adhering to gabion wire specifications is paramount for ensuring the creation of strong, efficient, and sustainable structures. Through expertise and adherence to industry standards, professionals in the construction and landscaping fields can deliver projects that stand the test of time while also respecting the environment. Whether it’s for a cost-effective retaining wall or an aesthetically pleasing garden feature, the right gabion wire will always offer reliability and performance that clients can trust.