Welded wire mesh, often referred to as 1 2 welded wire, signifies a fundamental component in many industrial and construction applications. This versatile material combines strength, durability, and cost-effectiveness, making it a staple in structural reinforcement, fencing, and industrial storage solutions. To truly appreciate its significance, one must consider the tangible benefits it provides and the extensive expertise surrounding its optimal usage.
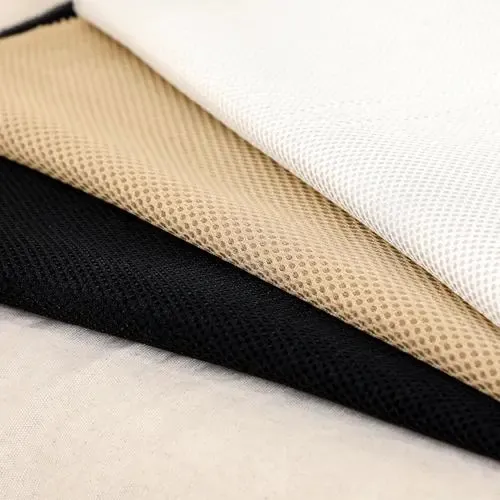
With years of real-world application and professional insight, one can discern the multifaceted advantages of 1 2 welded wire. In construction, its primary role is in reinforcement. The consistent spacing and uniform cross-section of the wires enhance concrete’s tensile strength. This addresses one of concrete's primary weaknesses—tensional loads. Moreover, welded wire mesh's prefabricated nature allows for easier fitting and placement on site, reducing labor costs and installation time while ensuring structural integrity.
In urban landscapes, welded wire meshes have increasingly become essential in modern fencing solutions. Their rigid and unyielding form ensures maximum security. However, they also possess a certain aesthetic quality—allowing for visibility and light passage while serving as a sturdy barrier. This dual-purpose nature helps in securing residential houses, animal enclosures, and perimeter fencing for industrial sites. It offers security without the claustrophobic feel of opaque barriers.
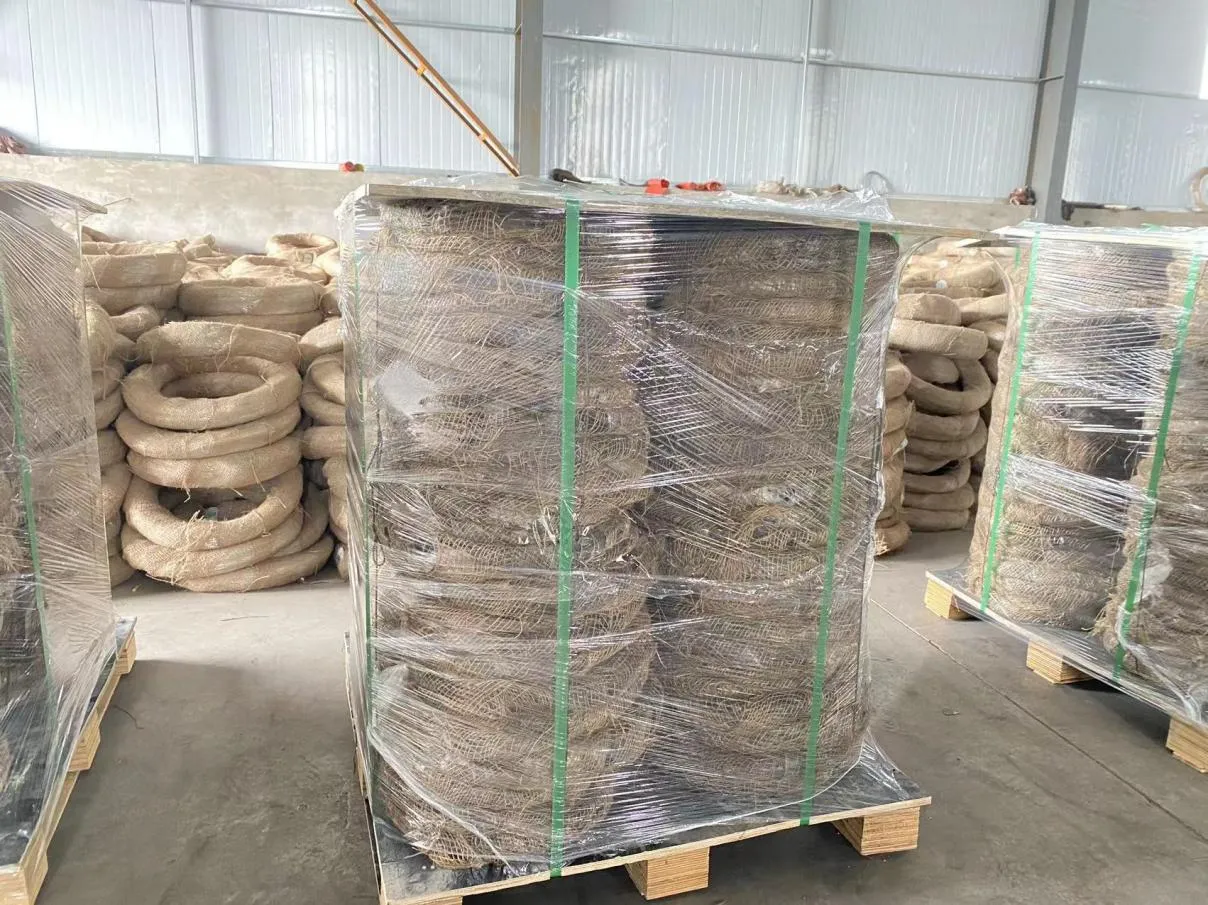
Industrial shelving and storage systems face unique challenges. Here, 1 2 welded wire shines with its combination of lightness and robustness. Backed by expertise in material science, manufacturers have optimized the mesh design to sustain heavy loads. This allows warehouses to maximize vertical storage without compromising on safety. The open structure of the mesh also ensures increased airflow, which is crucial in environments where humidity control is of essence, like in food or pharmaceutical storage.
1 2 welded wire
Environmental considerations have thrust 1 2 welded wire into the realm of sustainable infrastructure development. There is a growing trend towards using recycled materials in manufacturing processes. The steel used in these meshes often comes from recycled sources, reducing the carbon footprint associated with their production. This aligns with global sustainability goals and offers companies the chance to enhance their corporate responsibility credentials.
Trust is a critical factor when specifying welded wire for any project. Understanding the rigorous testing processes these products undergo can assuage any concerns regarding their durability and safety. Independent laboratories often conduct tensile strength, corrosion resistance, and load-bearing tests. These certified results provide peace of mind to engineers and architects, ensuring that the solutions they specify will stand the test of time.
However, the true authority in welded wire applications comes not just from understanding its composition but also its adaptability. Customization is key. Manufacturers often provide tailor-made meshes that can suit specific project needs, whether that involves altering the grid size for a unique architectural feature or applying coatings to enhance longevity and resistance to elements.
In conclusion, 1 2 welded wire is not merely a commodity, but a crucial component that underpins structural stability, security, and sustainability across various sectors. Its versatility and reliability are well-documented in professional circles, bolstered by comprehensive testing and a commitment to quality assurance. As the demand for efficient and trustworthy construction materials grows, the expertise and authority found in the welded wire mesh industry will continue to expand, offering innovative solutions for future challenges. Ensuring the selection and application of the right specifications tailored to project requirements remains essential in leveraging the full potential of this robust material.