Hot dipped galvanized mesh stands as a paragon of industrial innovation, a material that exemplifies both functionality and longevity. This unique product, celebrated across various sectors, embodies the quintessence of modern engineering by offering unparalleled resistance to corrosion and wear. Its application spans from construction projects to agricultural fields, providing robust solutions in every environment.
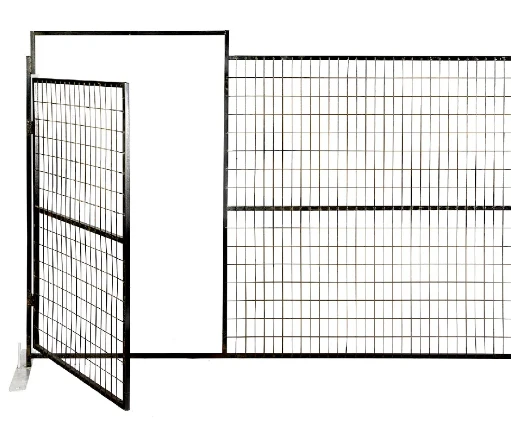
Years of technological advancement have culminated in the creation of hot dipped galvanized mesh, where expertise combines seamlessly with precision engineering. The galvanization process involves immersing the steel in molten zinc, forming a protective coating that guards against the elements. This layer is a critical factor in its resilience, allowing structures to withstand environmental stressors such as moisture and extreme temperatures over extended periods.
In terms of practical experience, hot dipped galvanized mesh is lauded for its exceptional durability and adaptability. Industries ranging from architecture to agriculture have turned to this material for projects requiring dependability and long-term service. For instance, the construction industry heavily relies on galvanized meshes for reinforcing concrete structures, offering stability and resistance that are critical to the integrity of buildings and infrastructural projects.
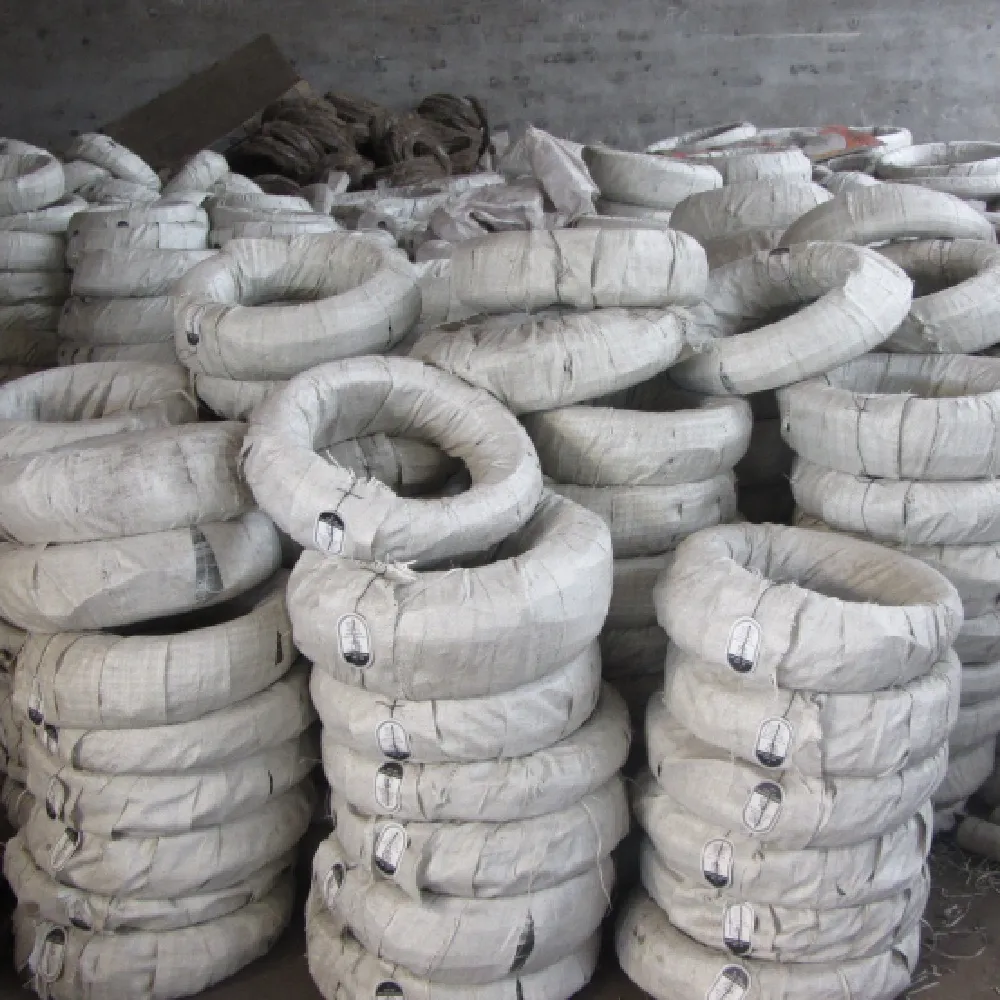
From an expert’s viewpoint, the galvanization process itself speaks volumes of its sophistication. Heat plays a crucial role as steel is submerged in the zinc bath, which is maintained at temperatures around 450°C. This interplay of heat and chemistry forms an alloy that effectively bonds zinc to steel on both molecular and surface levels. The result is a mesh that is not only coated but intricately integrated with zinc, offering superior surface protection that is vital for environments exposed to harsh conditions.
hot dipped galvanized mesh
Authoritativeness in the context of hot dipped galvanized mesh is derived from its ubiquitous application in regulatory frameworks and construction standards. Organizations and institutions often reference the material as a benchmark for safety and quality, underlining its importance and reliability. Standards such as ASTM (American Society for Testing and Materials) have set rigorous guidelines ensuring the production meets stringent criteria for resilience and structural integrity, a testament to its role as a staple in industry-standard practices.
Furthermore, trustworthiness is inherent in hot dipped galvanized mesh due to its proven track record in various industries. Long-term studies and field applications underscore its ability to provide lasting protection, reducing the need for frequent replacements or repairs. This reliability not only lowers maintenance costs but also enhances project sustainability by extending the life cycle of installations, a crucial consideration in contemporary resource management and environmental stewardship.
From a product perspective, selecting hot dipped galvanized mesh is a commitment to durability and performance. When procuring this material, it's essential to consider factors such as the gauge of the wire, the size of the mesh openings, and specific coating thickness to ensure optimal performance for intended applications. Customization options are also available, allowing end-users to tailor the product to meet specific project requirements, thereby maximizing efficiency and effectiveness.
In essence, hot dipped galvanized mesh is more than just a component; it is an investment in quality and resilience. The synthesis of experience, expertise, authoritativeness, and trustworthiness into one product ensures that businesses and industries can rely on it to uphold standards and exceed expectations. This synergy of qualities not only affirms its standing in today's market but also secures its relevance in future innovations and advancements.